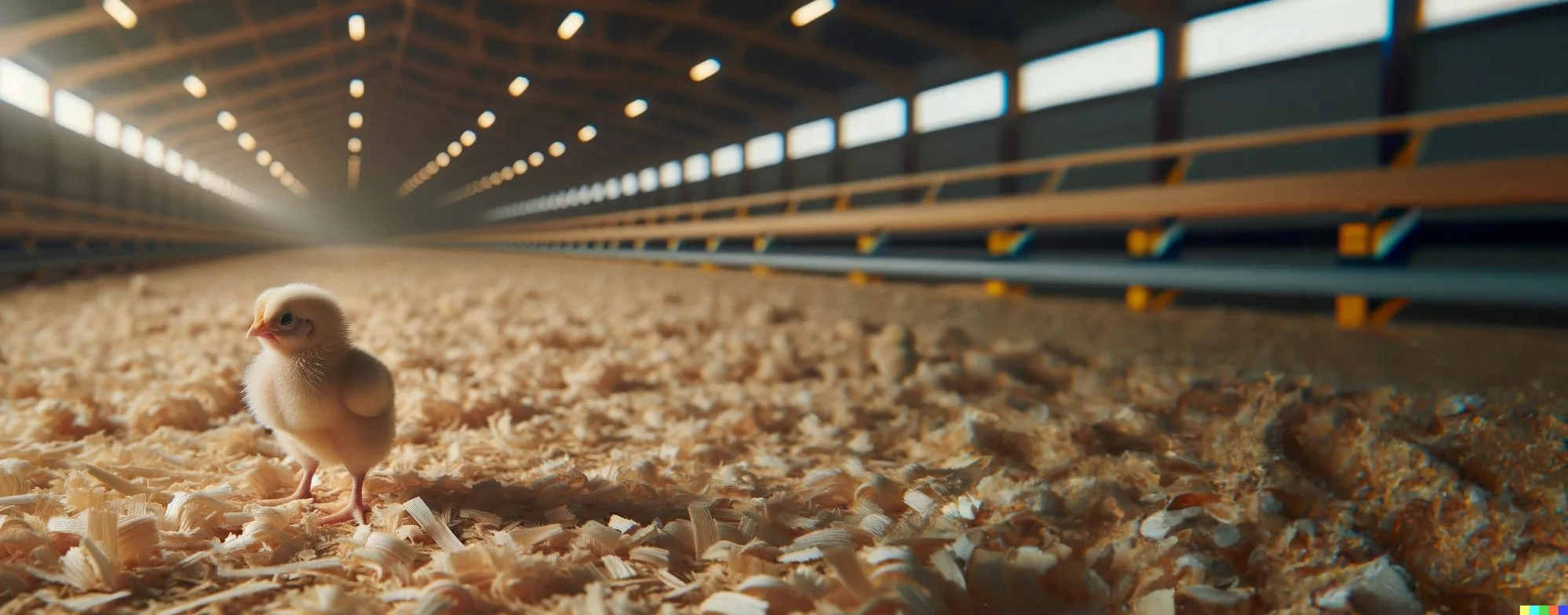
On-Farm Hatching
A new innovation could allow poultry producers to avoid stressful handling and processing of day-old chicks, while increasing productivity, lowering antibiotic use, and increasing supply chain flexibility.
The transport of live animals is widely recognized as a major challenges for animal welfare. During transport, animals generally don’t have access to food, water, climate control, or enrichment, resulting in particularly high levels of stress, especially when weather conditions are unfavorable.
The transportation of day-old chicks in the poultry industry is no exception. At a hatchery, chicks are generally hatched in a dark and noisy environment with high levels of dust. A batch of new chicks may take up to 2 days to hatch, during which time they might not have access to food or water, instead subsisting on their remaining yolk sac. Hatching is then followed by a series of stressful processing steps such as sexing, sorting, vaccination, and beak treatment. Chicks are then loaded onto a truck and transported to their rearing facility, which can be many miles from the hatchery. The chicks which hatch earliest may go without food and water for up to 4 days.
On-farm hatching is an innovative new practice being pioneered for broilers in Europe. With this technology, eggs are transported from the hatchery directly to the farm on day 18 of incubation, when they would traditionally be moved from the setter to the hatcher. Chicks then hatch directly in their rearing facility, bypassing the stressful processing and transportation that are a traditionally part of the hatching process. The European Food Safety Administration recommends on-farm hatching because it increases animal welfare due to the elimination of this handling stress.
Benefits
Without post-hatch processing and transport, chicks have immediate access to food and water, which has benefits for both animal welfare and production efficiency. When a chick can start eating right away, it will start gaining weight sooner, leading to an increase of up to 4.4% in slaughter weight.
Immediate access to feed and water also allows for better intestinal development which, combined with the lack of exposure to pathogens during hatching and transportation, means significantly less antibiotics may be required. One study found the use of on-farm hatching resulted in a 5.6 times lower probability of antibiotic use.
Studies have also consistently shown improvements in the rates of footpad dermatitis a condition characterized by painful lesions on the feet of birds, although interestingly the mechanistic reason behind these improvements remain unclear. Overall mortality is also shown to decrease by up to 18%, potentially linked to a reduction of dehydration and malnutrition from transport. In the case of on-farm hatching, a healthier and less-stressed bird is a more productive bird. These benefits may compound in countries like the US where transportation times are longer. Research indicates that the benefits like weight gain are linearly related to time spent in transport.
Hatchability has also been shown to consistently increase with on-farm hatching, with one study showing almost half as many unhatched eggs compared to a traditional hatchery. At a hatchery, eggs must hatch within a defined window, inevitably leading to some eggs which don’t hatch in time. With on-farm hatching, there is no restriction on when eggs can hatch, leading to this consistent increase in hatch rates.
On-farm hatching also potentially enhances the flexibility and robustness of the supply chain. Typically, hatcheries don’t hatch new chicks on every day of the week. This is because the hatching process can be labor intensive, and equipment needs to be cleaned in between hatches. Processing plants receiving the birds generally run more frequent shifts, meaning that some of the birds might be a couple of days older or younger than is optimal. On-farm hatching, however, allows for eggs to be transported to the farm and hatched on a more flexible schedule. This can lead to a more efficient and resilient egg supply chain, with birds being processed at a more consistent and ideal age.
Challenges
There are a few potential challenges producers must think through before adopting on-farm hatching. While on-farm hatching saves labor at the hatchery, some of this labor needs to be made up on the farm. Farmers must maintain precise climate control before and during the hatching process, and will sometimes need to make additional investment in climate controls. Farmers are also responsible for identifying and humanely euthanizing unviable eggs or unhatched chicks, which is critical for maintaining high welfare standards. Additionally, the farmer must lengthen the growout period by around three days to accommodate hatching. These challenges are weighed against the benefits to feed efficiency, slaughter weight, antibiotic use, hatchability, and welfare.
On-farm hatching may also be incompatible with other hatchery processing steps, such as beak treatment, vaccination, or sexing. However, many of these steps can be eliminated or transitioned to in-ovo solutions. For meat producers that desire separate sex rearing due to strict requirements around target weight, on-farm hatching might not be an option in the short term. However, in-ovo sexing on day 18 may make this possible over the longer term, once in-ovo sexing is substantially cheaper.

Market Overview
There are four companies currently in the market, each with unique approaches to on-farm hatching.
Nestborn, a Belgian company, has developed a machine that can automatically removes the hatching eggs from setter trays and places them directly on the litter bed in the barn. This machine is transported to the barn along with the hatching eggs. To ensure that conditions inside the barn are suitable for hatching, Nestborn also developed a device which can continuously monitor the temperature of the eggshell as the eggs hatch. The main benefit of this model is that no modifications are needed to the barn which means that farmers can implement on-farm hatching with minimal capital expenditures.
Vencomatic, a poultry equipment company based in the Netherlands, offers two on-farm hatching solutions called Patio and the X-Trek. With the X-Trek system, egg trays are set on a rail system that is suspended from the roof of the barn. This system is lowered down to the barn floor for the hatching process so that the newly hatched chicks can safely fall onto the litter bed on the floor. Once the hatch is complete, the rail system is hoisted back up to the ceiling.Patio, in contrast, is an entire barn solution, where platforms are stacked vertically and the chicks hatch and are reared on a single platform until harvest. One important benefit of Vencomatic’s approach is that many parts of the process are automated (e.g. the collection of unhatched eggs and egg shells), mitigating the potential increase in labor that on-farm hatching entails.
One2Born is another Dutch company that has developed a lower investment on-farm hatching solution. Their system revolves around a recyclable egg tray, called a hatchholder, that is placed on the barn floor. Hatching eggs are transferred to these hatchholders at the hatchery, which are then transported to the barn and simply laid on the barn floor. The design of the hatchholder allows air to flow around the egg shell for better hatching conditions, and keeps the eggs off the floor for better temperature control. As the eggs hatch, the hatchholder is be left on the litter bed where it serves as enrichment for the chicks and eventually biodegrades. This system requires minimal investment at the barn, and is optimal for biosecurity, since nothing is transferred between barns.
Home Hatching also has a simple approach: stainless steel folding frame stands on which the egg trays sit. Unlike other approaches, Home Hatching provides an infrared heater which sits above the stands so that the entire barn does not need to be preheated before the hatching eggs arrive.
Commercial status
Though some of the technologies that assist with on-farm hatching have been utilized for over a decade, there has been increased interest in the last few years. Across the EU, where on-farm hatching is most prevalent, there are over 500 million broilers that are hatched on-farm each year, primarily using Vencomatic and Nestborn systems. This means the total EU market penetration is at least 8%. This adoption was primarily driven by chicken meat producers seeing the production benefits to their operation, although the European retailer Colruyt Group mandated on-farm hatching across their supply chain for animal welfare reasons.
Other companies around the world are also starting to take notice. Some producers in Canada and Russia also use the technology, and major companies like Perdue are considering implementing on-farm hatching in their operations.

Layers
Thus far, on-farm hatching has been adopted primarily by broiler producers in Europe. For egg producers, a key barrier to on-farm hatching has been the need to sort chicks by sex after hatching. Male chicks are culled in the egg industry since they cannot lay eggs. However, in-ovo sexing is increasingly allowing egg producers to only hatch females, eliminating the need for post-hatch sorting. The male eggs could be removed before hatching, while the female chicks could then hatch on-farm. Read more here.
While the literature on how on-farm hatching affects layers is still developing, studies suggest that egg producers would still benefit from the demonstrated improvements to hatchability, mortality, antibiotic use, and reduced stress shown in the literature for broilers. However, some studies also suggest that reducing early-life stress, a prominent effect of on-farm hatching, can directly increase the production characteristics egg producers care most about: the amount and size of eggs that a hen produces.
One potential bottleneck to adopting on-farm hatching in the egg industry is that sorting by sex isn’t the only important processing that happens at the hatchery - vaccination and beak treatment are also common. However, both of these have potential solutions. In-ovo vaccination, the practice of injecting an unhatched egg with a vaccine, was also traditionally difficult for layers, since all of the vaccines used on the male eggs went to waste. However, in-ovo sexing could similarly enable in-ovo vaccination for layers, so they can be hatched on-farm. The vaccine for Marek’s disease is the main one which would need to be moved in-ovo, which should not be problematic given that this is the current practice for broilers. Regarding beak treatment, reduction in early-life stress due to on-farm hatching could itself reduce the prevalence of injurious pecking, and hence the need for beak treatment.

Frequently Asked Questions
-
Since eggs occupy less space than hatched chicks, transporting them to the farm is more space-efficient. This potentially reduces the number of trucks or flights needed, decreasing the carbon footprint of poultry production.
-
Many modern hatcheries use systems such as HatchCare, where chicks are hatched at the hatchery, but then have immediate access to food and water in the hatcher incubator. Numerous studies have examined the relative effects of hatchery-hatched chicks, on-farm hatched chicks, and chicks hatched in systems like Hatchcare. In general, the findings have been that systems like Hatchcare capture some, but not all, of the benefits of on-farm hatching since chicks still undergo early life stress due to processing and transportation.
-
On-farm hatching systems should be used in conjunction with effective candling systems to identify any eggs which may be unviable before they are transferred to the farm. However, it’s inevitable that there will be some number of unhatched eggs or unviable chicks. In these cases, it’s critical that the farmer be diligent about identifying and euthanizing the birds that will never be productive. Small macerators or gassing chambers are readily available for this purposes, and on-farm hatching companies will sometimes provide this equipment directly to farmers to facilitate this.
-
Some studies suggest that chicks hatched on-farm score lower on traditional measures of chick quality, such as naval and hock scores. However, it’s important to note that none of these studies found an associated increase in mortality, or decrease in productivity that is often associated with lower chick quality. For on-farm hatching systems, traditional measures of chick quality may therefore be less applicable, although this is an important area of future research.